Holistic Factory Planning for a New State-of-the-Art Battery Factory
Synchronize factory and object planning
The detailed planning process is based on the selected preferred variant from concept design and is designed to ensure that all user requirements are met and ready for implementation. From a factory planning perspective, the focus is on the detailing of the layout down to equipment level, the detailed planning of the production logistics and warehouse structures, the final documentation of all user requirements and the integration of the factory and building layout.
Ideally, the principle of synergetic factory planning is transferred from theory to practice at this point and planning is driven forward with close integration of factory and object planning. The BIM methodology optimally supports this approach by developing a planning model as a central information carrier for all trades.
BIM and factory planning
Adopting a BIM methodology allows you to streamline the collaboration of all trades involved in the construction of your factory, thereby offering significant advantages. The aim is to use a leading model to establish a central information carrier (single point of truth) across all planning phases in order to avoid information asymmetries between the planning statuses of the individual trades. The central planning model is subject to continuous enhancement and further development at defined points in time, with the specialist models and associated information being integrated via standardized interfaces. Thanks to the centralized logic, the required information can be called up and used at any time according to individual needs and current status.
The BIM methodology enables the achievement of added value through high-level coordination and synchronization, both in the detailed planning phase and during subsequent implementation. It also provides the foundation for the use of a digital twin of your factory in subsequent operation.
Trust through Projects
Our success stories
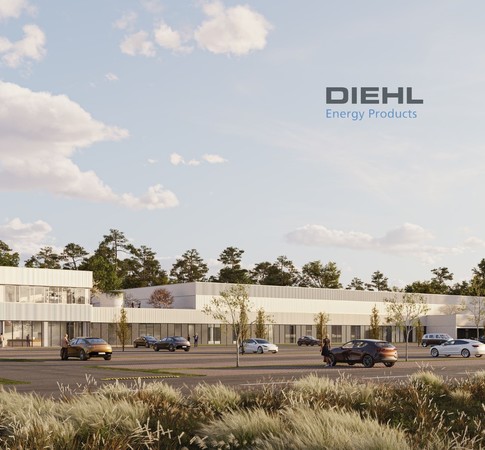
Workplace guideline (ASR) and safety specifications in the detailed layout
The transfer of the concept layout into a detailed layout requires the final positioning of all workstations and equipment, the layout of the provision, buffer and storage areas and the detailing of all peripherals. Functional requirements, such as material flows, play a central role in the final design.
Nonetheless, the protection of people and materials must be ensured without fail, regardless of functionality. We take core issues of the workplace guideline such as escape routes, path widths and fire protection requirements into account when designing the detailed layout. It is equally important to consider the well-being of employees in the workplace, with regard to factors such as temperature, ventilation and lighting. In addition, there are process-specific or company-specific security requirements that must be integrated into the detailed planning phase. Restricted area access, separation in the warehouse structure or the handling of hazardous substances are just three examples from a large number of individually possible safety specifications.
Production logistics in the detailed planning phase
Depending on the degree of automation of the production logistics, the scope of the project may justify a separate project. Thanks to our interdisciplinary expertise in the areas of factory planning, logistics planning and general planning, we are able to plan even highly complex subsystems with structural implications in detail. In making recommendations regarding the optimal system, we place significant emphasis on achieving an appropriate balance between functionality and economic efficiency.
However, the production logistics system not only frequently results in interfaces to object planning, but also and in particular to IT. We facilitate the integration of processes into your system landscape by providing comprehensive descriptions of new or modified processes and collaborating with your IT department to define the essential parameters for planning and control.
Sustainability in the detailed planning phase
To create a green factory, the key components should have been defined well before the start of detailed planning and justified by a multidimensional assessment. However, the implications become pervasive during the detailed planning phase, as it is essential to align the factory planning with the technical implementation planning of all key elements of the green factory.
The required infrastructure and the corresponding media supply points must be located at the workstations and equipment in the layout. We recommend close cooperation with the object planning department in order to harmonize the optimum technical design with the required functionality. Furthermore, the utiliuzation of renewable energy sources frequently necessitates a modification of production planning and control principles, which factory planning must address at the outset.
User requirements:
From height requirements to energy connection loads
The structured recording of all user requirements is not a time-related task, but rather extends over the entire planning period and reaches its final granularity in the detailed planning phase. The importance of this task is fundamental, as the requirements defined by the factory planning phase form the basis for the planning of the other trades.
Here too, the BIM methodology offers a major advantage, as all requirements can be directly attributed in the model from the start of planning and with increasing granularity. This makes parallel maintenance of information in different formats redundant. Initially, attributes such as dimensions, heights and loads are assigned to the defined room structures in order to successively assign all requirements to the equipment as the level of detail in the layout increases.
Factory Realization
Preparation and support for factory realization
The transition from the detailed planning phase to preparation of realization is usually fluid and the level of boundaries depends on the time pressure in the project. It is important to draw up an implementation roadmap in order to create transparency for all project participants regarding the milestones and the critical path. It is the responsibility of the factory planning team to oversee the implementation of the plan by the executing trades, using structured monitoring to identify any potential issues at an early stage. Participating in cross-trade meetings in the context of the selected award procedure is an integral part of our service offering, along with providing support to clients during the plan review process.
To meet the fixed start of production (SoP), new or substituted investments in equipment must be made in parallel with the implementation of the factory. The overall schedule must take into account the complexity and individuality of the procurement process, allowing for the necessary activities to be initiated at the appropriate times. The initial step is to define the functional specifications for the procurement requirements. This will then inform the subsequent tendering and awarding process. From a production based point of view, requirements can be classified into three categories.
- Standard operating resources
- Special equipment
- Logistical subsystems
FAQs about Detail Planning
How can functional and structural requirements be optimally combined in a single plan?
Successful interaction between processes and buildings determines the success of factory operations. The greater the impact of the process requirements on the building, the more complex the interaction becomes during planning. With the help of the BIM methodology, we implement a “single point of truth” in the planning process, whereby all requirements are documented centrally at a geometric and informational level. On the one hand, this significantly reduces the number of interfaces during planning, while on the other, it creates the optimum basis for the trades carrying out the work - both from a structural and functional perspective.
What aspects need to be taken into account in the detailed planning that are often considered far too late?
The importance of successful interaction between factory and building planning has been successfully manifested in many industrial construction projects, at the latest with the establishment of the scientific approach to “synergetic factory planning”. However, in order to ensure successful factory operation immediately after the realization of the building, further topics must be considered at an early stage:
- Early initiation of time-critical procurement processes (machinery and equipment, logistical equipment, etc.)
- Detailed planning of the required IT infrastructure and relevant interfaces
Consideration of possible interim solutions (relocations from existing structures, parallel operation, etc.)
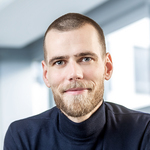
Simon Vehof
Business Development Manager
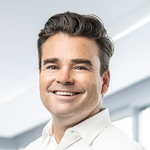
Matthias Göke
Managing Partner
Dr. Norbert Szimhardt // Head of Engineering and Product Management